【プラズマ効果事例】樹脂バックドア接着前工程への適用
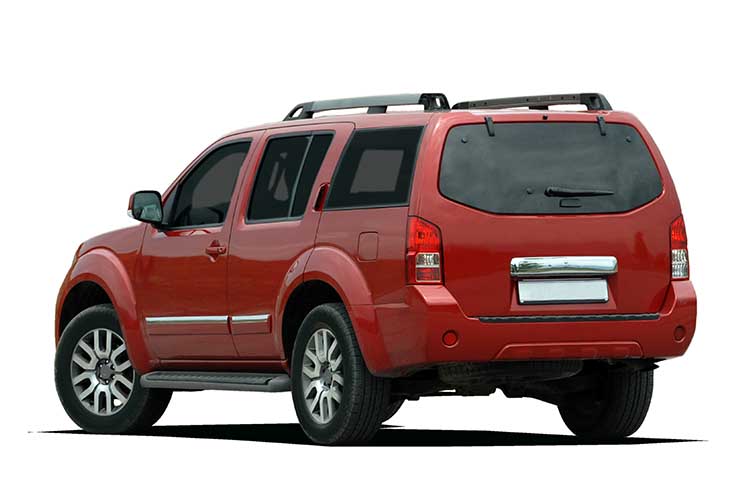
近年、自動車排出ガスによる環境汚染が問題となっており、温室効果ガス排出量削減を掲げた「パリ協定」が採択されました。その結果、低燃費自動車や電気自動車の開発が各メーカーにより急速に進められております。
低燃費化や電気自動車の課題である走行距離を延ばすために車体の軽量化が進められており、車体を構成する部品の材質を従来の金属からアルミ合金や樹脂へ変更が行われています。
中でも比較的重量が重いバックドアの樹脂化が注目を集めておりますが、樹脂材料の多くは難接着性を示すため表面処理なしに接着することは困難です。
本記事では、難接着性を示す樹脂材料が採用される自動車の樹脂バックドアへの大気圧プラズマ装置「Tough Plasma」の適用例についてご紹介します。
1.はじめに
地球環境を守る対策として、低燃費化による自動車排出ガス削減や排出ガスを出さない電気自動車の開発が盛んに行われおります。
低燃費化や電気自動車の課題である走行距離を延ばすために部品の軽量化が注目を集めており、金属材料から重量が軽い樹脂材料への置き換えが増えています。
自動車部品の中でも比較的重量がある金属製のバックドアではリベットやボルトを用いて部品の接合が行われていましたが、軽量化に伴う樹脂材料の採用によって接着剤を使用した接着・接合技術が必要となってきております。
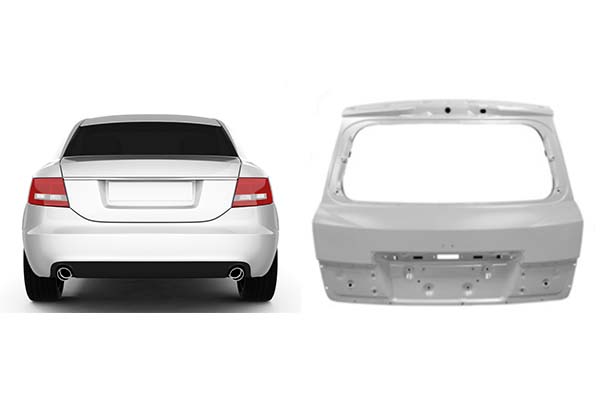
2.バックドア樹脂化の問題点
バックドアで採用される樹脂材料の多くは、難接着性を示すPP(ポリプロピレン)が用いられることがあり、接着剤を塗布する前に樹脂の表面改質を行う必要があります。
実際に表面処理していないPPに対して接着剤を塗布・硬化させ、引張せん断試験(JIS K 6850)を行うと界面剥離が起こります。

バックドア樹脂化に伴う課題
- 樹脂、ガラスの異種材料を接着・接合させる必要がある
- 使用される樹脂は、ガラス繊維や炭素繊維が複合された難接着性のPPが用いられている
3.プラズマ処理の効果
難接着材料の接着性向上にはTough Plasmaの使用が有効です。
プラズマ処理前後のPPを接着剤で接合し、引張りせん断応力試験による強度比較を行った結果、プラズマ処理前の引張りせん断応力値が0.1MPaに対し、プラズマ処理後は2.5MPaと25倍の強度が得られる事が分かりました。
また、基材の破断状態を確認すると、プラズマ処理前では、基材表面で界面剥離しているのに対して、プラズマ処理後では接着剤の凝集破壊となっている事が分かります。
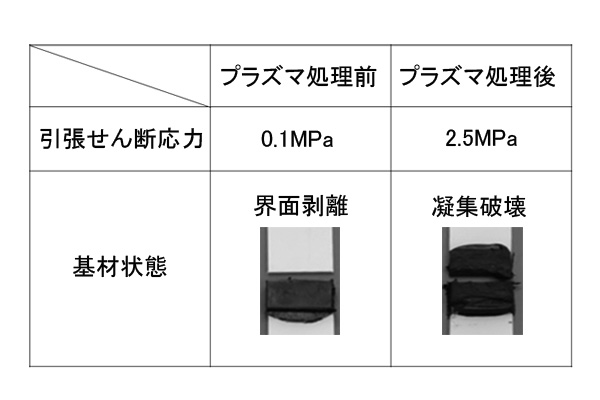
これは疎水性であった樹脂表面が親水性へと改質し、濡れ性が向上したためです。
PP樹脂のプラズマ処理前と処理後の濡れ性の変化は水接触角の結果からも確認できます。
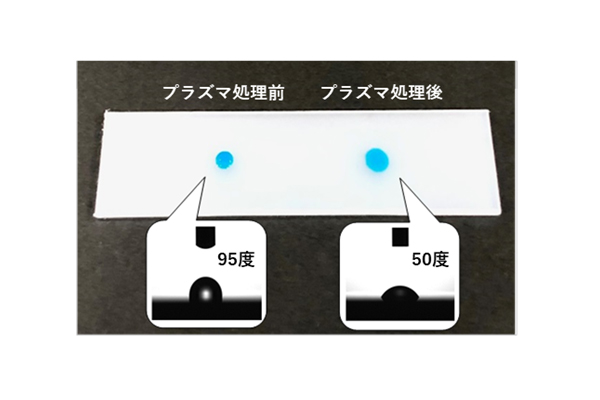
なぜ濡れ性が向上するの?
Tough Plasmaは電極間の放電による電気エネルギーによって酸素を反応性の高い酸素ラジカルに変化させます。
これを照射することで、酸素ラジカルが材料表面と反応し親水性の官能基が付与され、濡れ性が向上します。
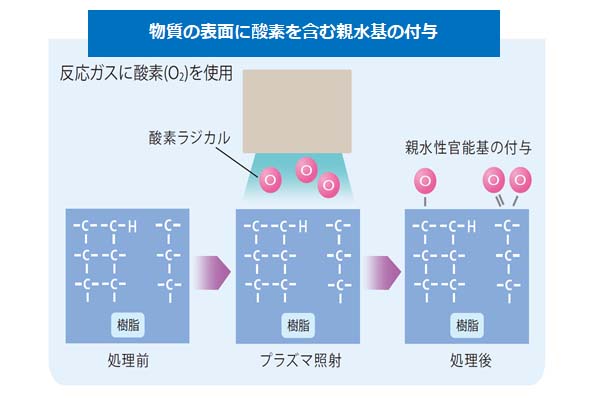
4.まとめ
樹脂バックドアで使用されるPP系樹脂にTough Plasmaで表面処理を行う事で接着強度の向上を確認する事ができました。
弊社ではお客様のご要望をお聞きし、最適なプラズマ処理方法のご提案をしております。Tough Plasmaによる表面改質技術のご採用を検討される場合はお気軽にお問い合わせ下さい。